Test Systems
PTO Test System
- Test system for Automobile engine (PTO) efficiency
- Control system – PLC – GE Fanuc, SCADA – Cimplicity
- VFD – PTO test with variable speed
- Observed parameters are
- SPEED – Motor and PTO Speed
- Vibration – PTO System Vibration
- Torque – PTO System
- Pressure – input and output Line pressure
- Temperature – PTO Engine Gear box
- Cimplicity SCADA for data monitoring and Presetting
- Data Logging and SQL Data base
- Graphical Representation (Trending graph) for Speed and Torque
- Alarm monitoring and controlling
Either Filling System
- This system for test automobile engine temperature gauge using either
- This test design and developed by electro pneumatic
- Either filling tube diameter 0.4 mm copper tube
- Either filling pressure 0.5 to 1.0 bar
- Vacuum Pressure in copper tube -720 mmhg
- System working, suck the vacuum pressure from copper tube and fill the either into tube for preset time
- This system working temperature – 20 – 25 Degree Celsius
- Machine working Pressure – 6 to 8 bar
- Working voltage – 24 VDC
- Provided Rigid Fixture for clamping and filling setup
- Provided Control system – Embedded Controller
- Provided Touch panel for parameter setting and production monitoring
- Provided Vacuum pump and digital Pressure transmitter
- Provided Pressure switch and FRL with Gauge for working pressure
- Provided Precision water valve for either filling line
- Provided Closed Container with glass tube for either filling line
- This system consist of fabricated SS table
Triple Plunger Pump Systems
- Test system for triple plunger pump efficiency
- Control system – PLC and Embedded
- Pump ON/OFF control with current sensing
- Observed parameters
- Pump discharge – using flow meters
- Temperature – pump and motor temperature
- Pressure transmitter – pump inlet water pressure
- Speed controller – motor speed
- Energy meter – motor input voltage, Motor current, and Power
- VB based front end graphical design for data monitoring and setting
- Data logging and SQL Database
- Trending line chart for flow, speed, pressure, and power parameters
- Alarm monitoring
Smart tester Coil Plate Leak Testing Machine
- Machine will be fabricated by rigid and fabricated structure
- Machine developed based on Electro pneumatic
- This system test method – Wet Test
- System consists of top arm with component clamping , Bottom with water tank and component Fixture with Punch setup
- Component Air Filling Volume 20 ml with 10 bar
- Control System PLC
- Provided pressure Booster pump for 6 bar into 12 bar
- Provided FRL with Pressure gauge for regulating Component test pressure
- Provided separate FRL with Gauge for Operating pressure
- Provided Pressure transmitter for monitor the leak in component
- Provided touch panel for parameter setting, monitoring the running data & I/O status , Data logging and Alarm logging
- Provided Safety Curtain Sensor for operator safety
- For Operator safety Provided Both hand Switch With Emergency setup
- Input Voltage – 1PH/220 V, Working Voltage – 24 VDC
- Provided Proximity sensor for UP/Down Position of water tank and top arm
- Provided tower lamp with buzzer given for system status
- Given transparent enclosure for safety and visible the machine status
Gripper Test Rig
Sed ut perspiciatis unde omnis iste natus error sit voluptatem accusantium doloremque laudantium, totam sam.
Features & Specification
- This system design and developed to test reliability of the gripper
- Machine will be fabricated by rigid and fabricated structure
- Machine developed based on Electro pneumatic
- System consists of Pneumatic clamping with Component up/down moment
- Component clamping pressure 6 bar
- Component up/down moment 6 bar with flow control adjustment
- Control System PLC
- Provided FRL with Pressure gauge for regulating Component clamping and moment
- Provided touch panel for parameter setting, monitoring the running data & I/O status , Data logging and Alarm logging
- Data logging in touch panel CSV file and given USB Exported option
- Input Voltage – 1PH/220 V, Working Voltage – 24 VDC
- Provided reed switch for UP/Down and middle position of component
- Provided tower lamp for system working status
- Given transparent enclosure for safety and visible the machine status
- Provided Vibration mount for the machine
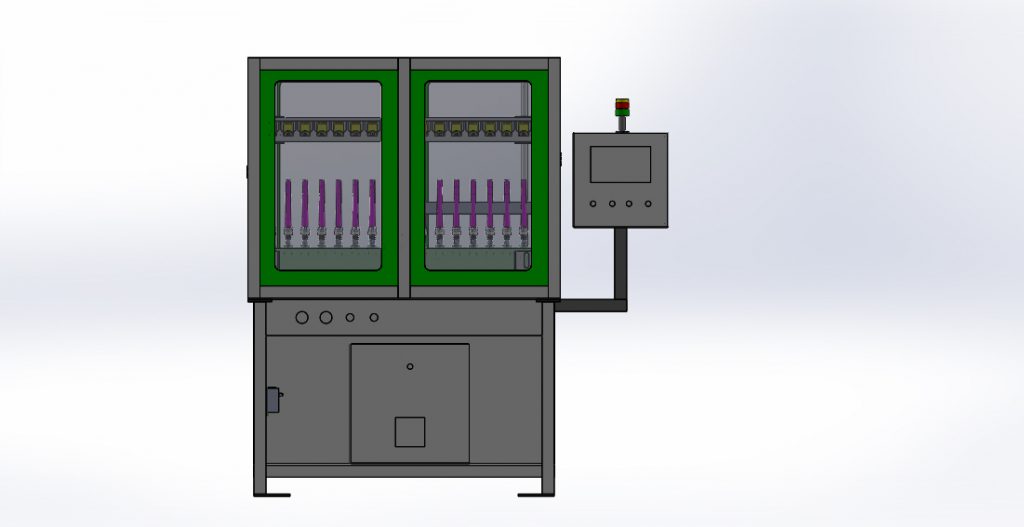
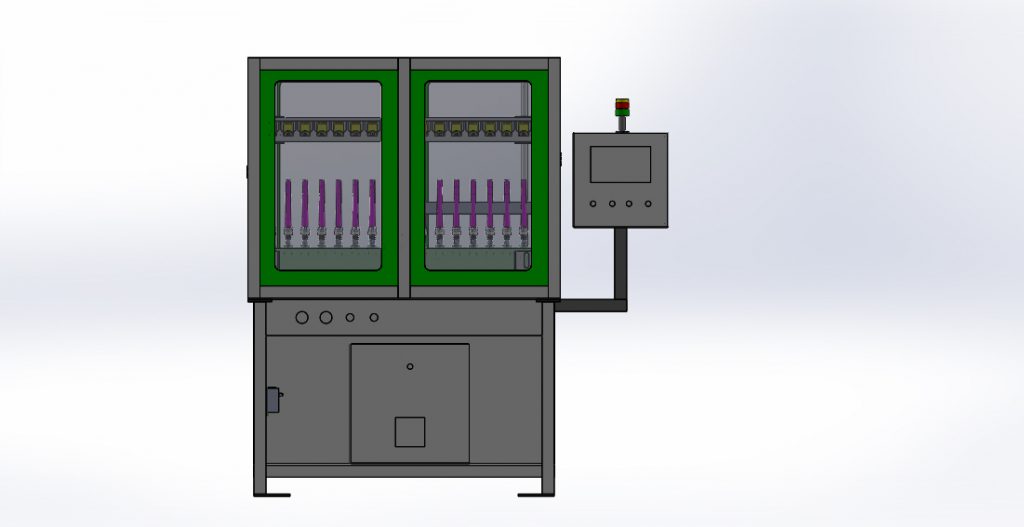
Break Reliability Test Rig
Sed ut perspiciatis unde omnis iste natus error sit voluptatem accusantium doloremque laudantium, totam sam.
Features & Specification
- This system Design and developed to test the reliability of the brake unit
- Machine will be fabricated by rigid and fabricated structure
- Machine developed based on Electro pneumatic
- System consists of Pneumatic actuator to lock and unlock the brake into spindle
- Machine working pressure 6 bar
- Component up/down moment 6 bar with flow control adjustment
- Control System PLC
- Provided FRL with Pressure gauge for regulating Component lock and unlock
- Provided touch panel for parameter setting, monitoring the running data & I/O status , Data logging and Alarm logging
- Data logging in touch panel CSV file and given USB Exported option
- Input Voltage – 1PH/220 V, Working Voltage – 24 VDC
- Provided sensor for RPM Calculating of each set of spindle (Speed – 30000 RPM)
- Provided VFD for Main spindle motor Speed Control
- Provided tower lamp for system working status
- Given transparent enclosure for safety and visible the machine status
- Provided Vibration mount for the machine
“The challenge is everywhere we invent a new technology, we are taking the test rig as challenge on respected domain and done it at best”
Thanga Krishnan
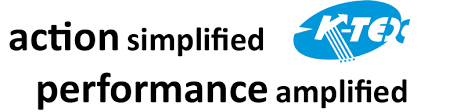